Collaboration and clear communication: these are two key ingredients of efficient, effective project delivery. Without them, progress is slowed and mistakes are made. To improve efficiency, many project teams have been using Design Assist (DA), a project delivery method in which the full project team—architects, engineers, contractors, and subcontractors—are engaged in the early stages of a project to improve coordination and optimize design solutions.
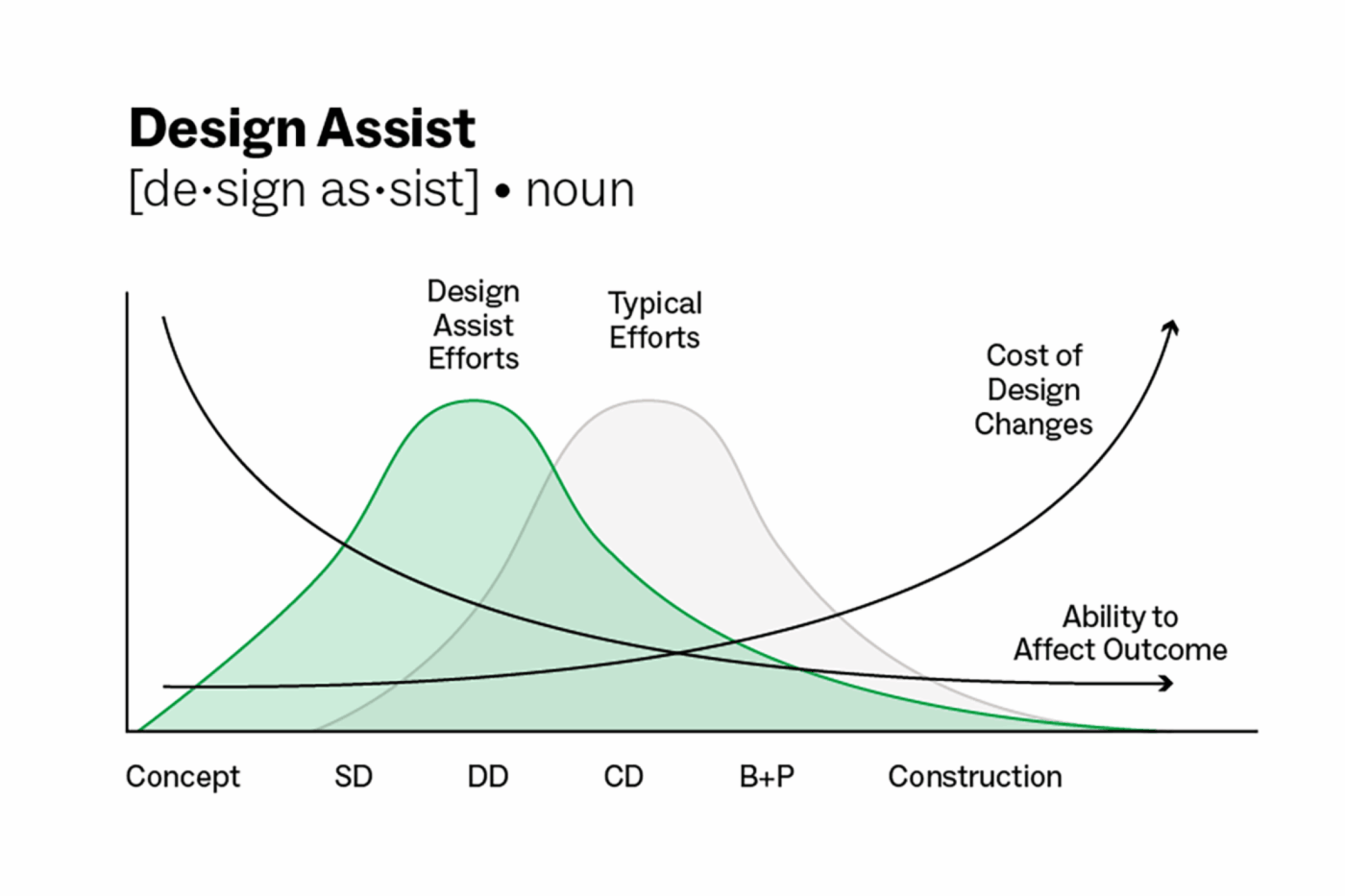
Some colleges and universities have a hard time employing Design Assist within the constraints of strict institutional procurement methods. Our work on the Forbes Beeler Residence Hall at Carnegie Mellon University offers an interesting case study and an argument in favor of working through potential challenges and pursuing DA: the client’s concerns were answered with a custom process; the project benefitted in several clear ways from the DA methodology; and the timing of the project during Covid gave us a unique opportunity to compare the performance of DA- and Non-DA trade partners.
Forbes Beeler Residence Hall—Project Background
Located in Pittsburgh’s Squirrel Hill Neighborhood, the 113,500-SF Forbes Beeler Residence Hall will provide apartment-style suites for upper-class students. Like much of Pittsburgh, the project site has incredibly steep topography, and the Institutional Master Plan imposed restrictions on the building’s height. The resulting design meets these constraints with a long footprint built on a complicated stepping foundation system.
Design Assist, Customized to Fit
The construction manager (CM) was engaged shortly after the design team to provide preconstruction services. At that time in 2019, a hot local construction market was straining contractor bonding and labor capacity, so the CM suggested engaging a handful of subcontractors in Design Assist agreements to help understand the current market and provide reliable cost projections. Although the owner was interested, the suggestion was met with concerns about risk, competitive pricing, and inflated costs. After careful deliberation, Carnegie Mellon was able to create a set of rules to move forward with an approved version of the Design Assist method; the team affectionately referred to this as “The CMU Special.” This custom form of Design Assist included the following:
- An RFP process requiring a minimum of three bidders.
- The provision of a Preconstruction fee for Design Assist work.
- An amendment in the subcontractors’ contracts for an “opt out” clause to allow the Owner to rebid the project at any time.
- “Open Book” accounting, billed as Time & Material, not to exceed.
- A detailed plan from DA partners demonstrating their strategy to achieve target design values.
- A shared savings plan with DA Partner as an incentive to DA partners to not inflate their cost. (Any accrued savings would be split fifty-fifty between the Owner and relevant DA partner.)
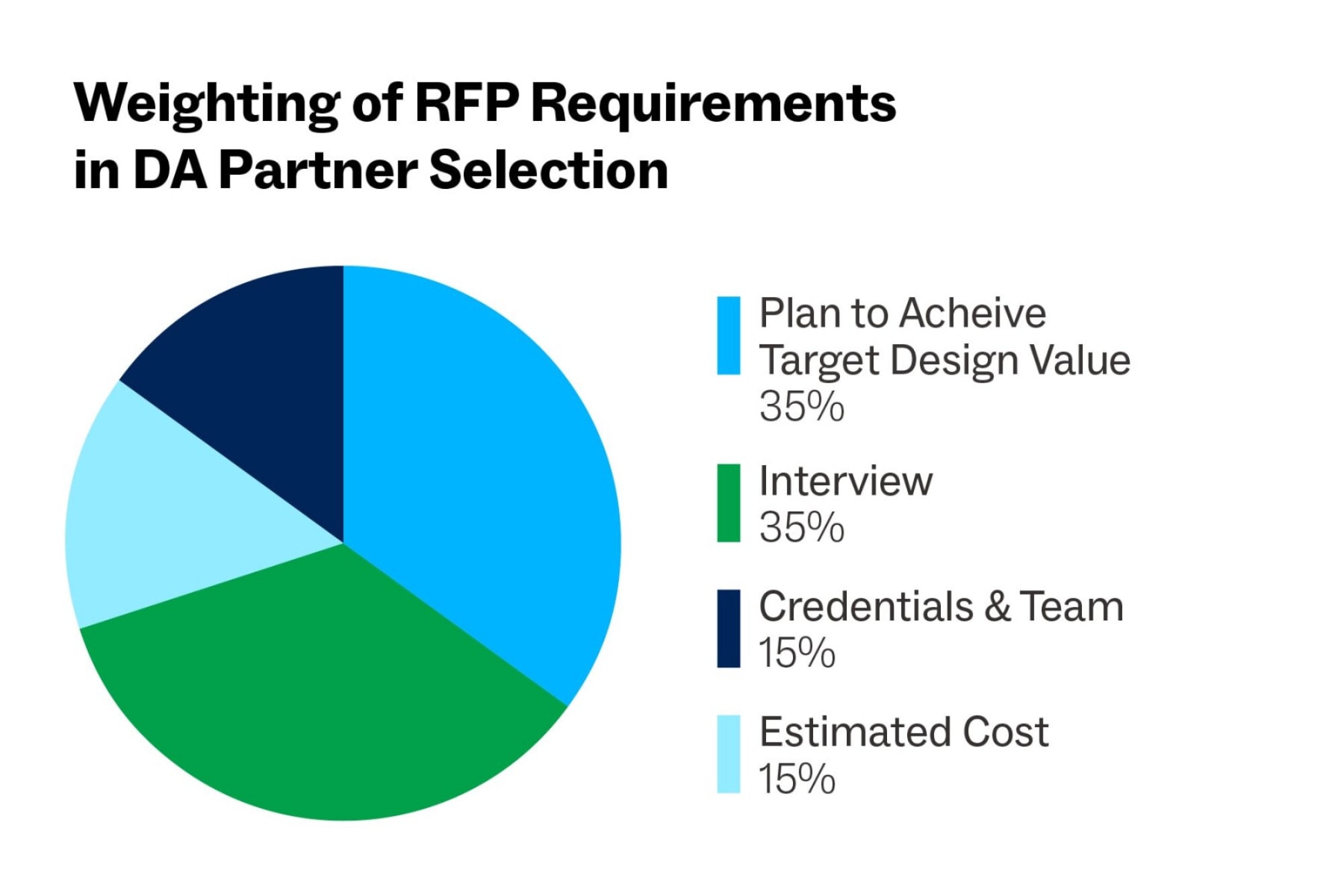
The RFP process for the DA partners began at the end of the Design Development (DD) phase, and subcontractors were invited to use the DD drawings for pricing. Carnegie Mellon’s selection process places several factors—including a partner’s interview and plan to achieve the target design value—above cost. All told, 11 Design Assist partners were engaged through this process.
Positive Design Impacts of the DA Process
The early engagement of subcontractors through the Design Assist process improved our project’s design and construction outcomes. In particular, the foundation systems, the use of bypass framing, and the selection of precast concrete panels helped to shorten construction duration, minimize risk, and improve the overall design.
Foundation Systems
Our design team originally specified cast-in-place concrete for the project’s foundation walls. However, when the masonry DA trade partner was brought into the design conversations, they immediately suggested that we switch from cast-in-place foundation walls to structural block walls. Through their intimate knowledge of the Pittsburgh construction market, they knew that concrete block was readily available and more cost effective than traditional cast-in-place concrete foundations. This design change impacted many details including brick ledges, coursing alignment for footings, curtainwall sill heights, etc. Making a change of this magnitude during construction—when this trade would normally be involved—would have had a major impact on design and schedule. However, due to the trade partner’s involvement in early design phases, it was comparatively easy to coordinate.
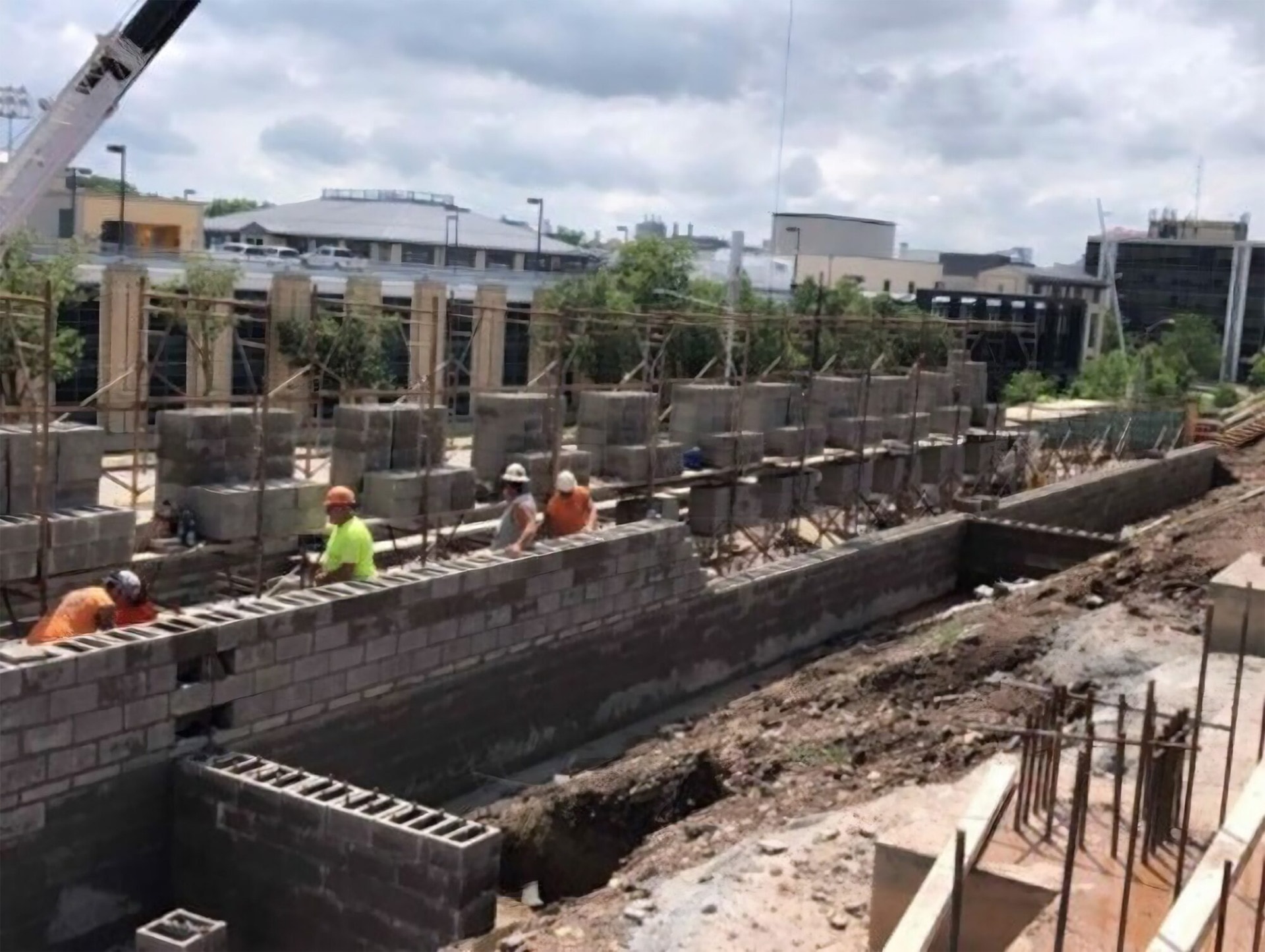
Bypass Framing: Prefabrication and Impacts on Critical Path
One of Design Assist’s biggest impacts on the project was in the exterior wall framing method. In conventional framing, a building’s concrete floor slabs are poured early, and the concrete has to partially cure before backup framing can be installed between slabs. Our framing DA trade partner proposed that we employ bypass framing instead. In bypass framing, the backup wall is assembled outside the slab, so there is no need to wait for concrete to be poured and cured before framing can start. It is a less typical framing method, but one that our trade partner had experience with and believed would save time and money.
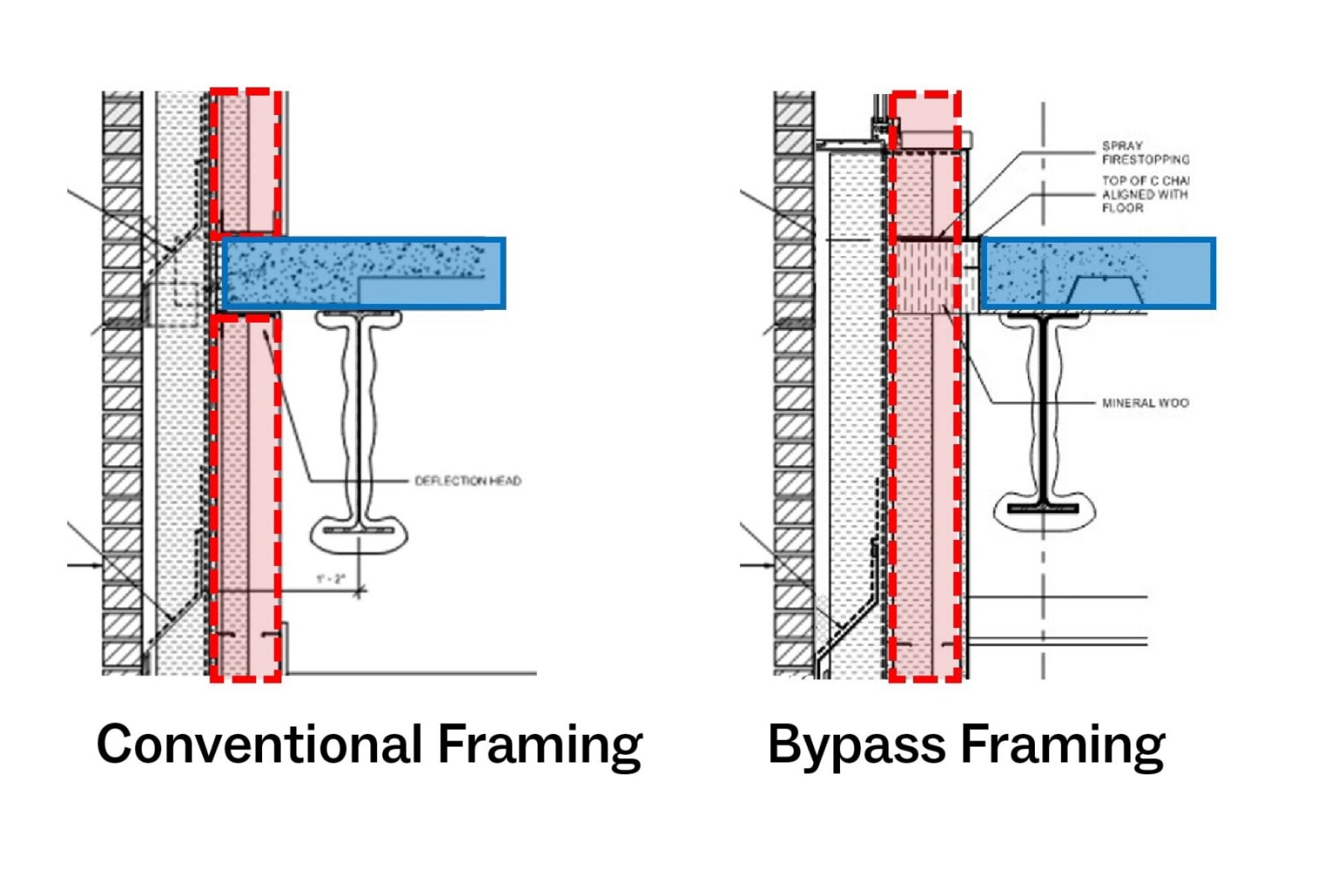
By employing bypass framing, we were able to prefabricate and install the backup walls before concrete slabs were even poured. Rebar and welded wire fabric layouts, slab penetrations, and shafts were all coordinated simultaneously with the panel installation. Because of this, the building envelope was largely enclosed by winter, thus reducing the need for temporary enclosure and heating for pouring slabs. Brick, curtainwall, and windows were able to be installed concurrent with pouring concrete. Through these efficiencies, our construction schedule was considerably shortened. Furthermore, prefabrication allowed a higher quality installation of the assembly’s air/vapor barrier, which was demonstrated in the impressive results achieved during the project’s blower door tests.
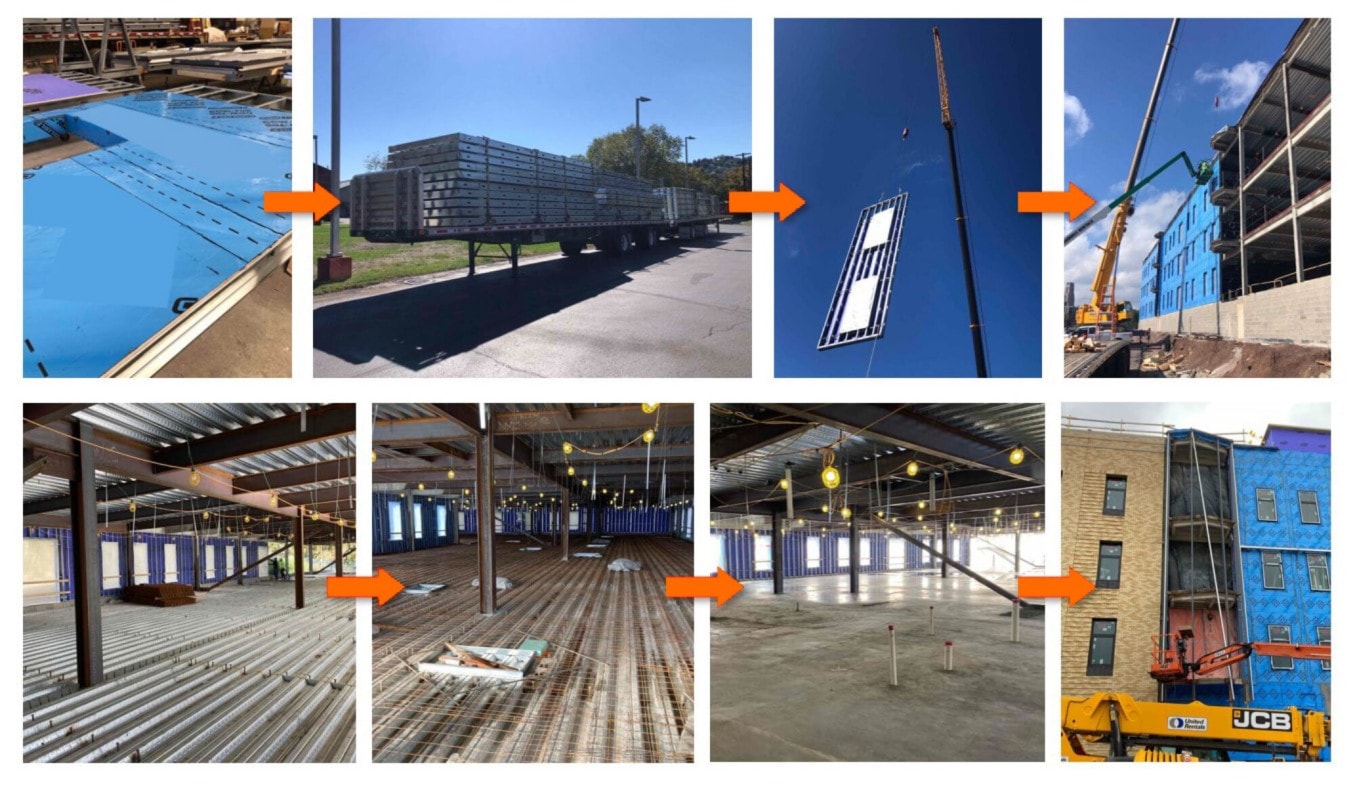
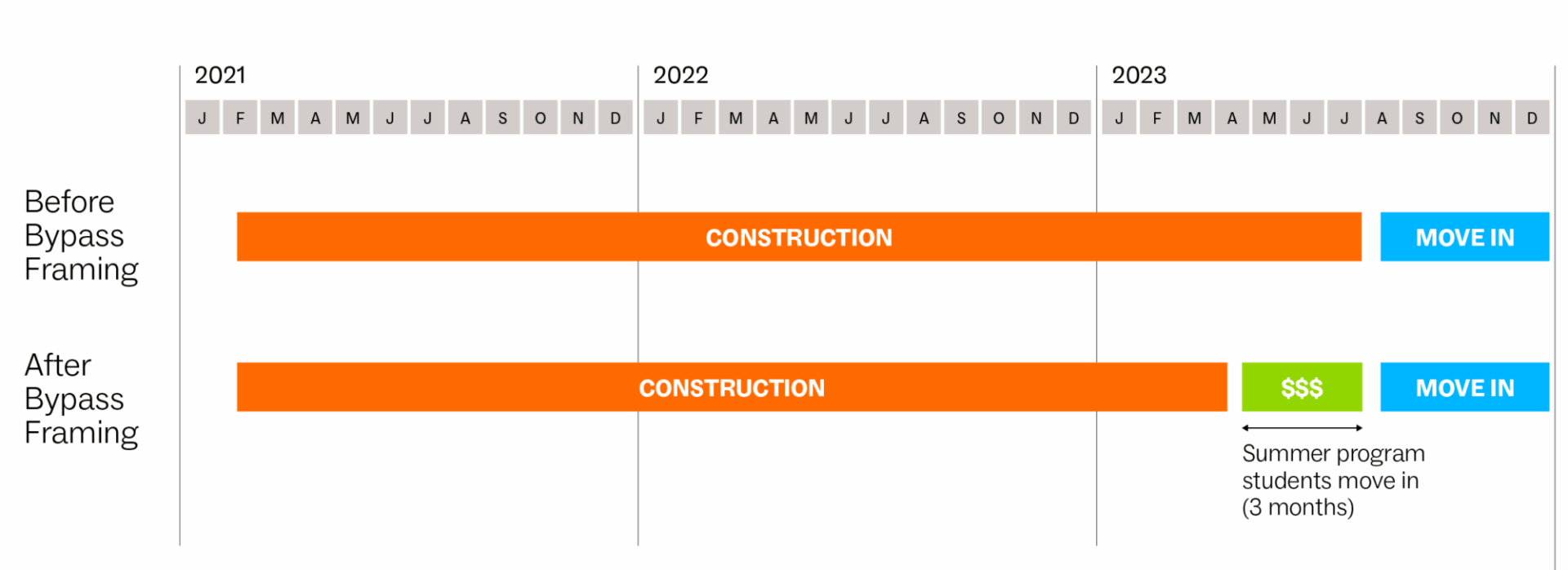
Precast Panels
The building’s exterior walls are largely made up of brick, with sections of precast concrete panels that required custom form liners. To assist in the complex detailing that these custom panels required, our masonry DA partner involved their precast fabricators during the design meetings. Precast fabrication subconsultants are frequently left out of design and construction conversation until after bids are awarded. However, the inclusion of this specialty early in the project helped our design team to optimize the length, width, and height of the panels, pinpoint relieving angle locations, and detail the panels’ complex chamfered projections. The input from these subconsultants also helped us optimize the design of the concrete panels in order to achieve a maximum amount of pattern variation with a minimum number of different form liners. This input not only made the fabrication easier and more streamlined, but it also helped our team refine the aesthetics of the facade.
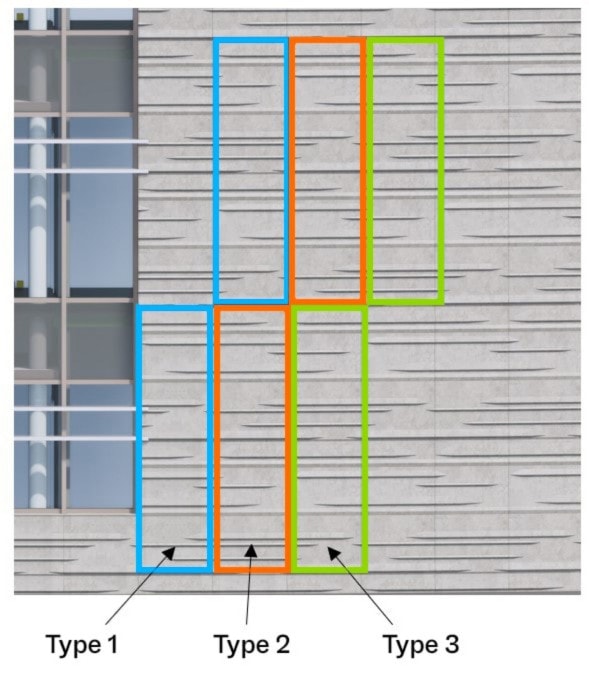
Comparing DA- and Non-DA Trade Partners
In April 2020, just as Construction Documents were going out to bid, Covid restrictions put the project on a ten-month hold. During that time, local construction slowed by roughly 60%. With the market in their favor, Carnegie Mellon decided to evoke the opt-out clause and re-bid the design-assist trade packages. Some of the DA trade partners were not re-awarded their bids; they were replaced with trade partners who had not collaborated with the team during Construction Documents phase.
Due to the custom “CMU Special” approach to the DA process, the construction manager was uniquely positioned to compare DA and Non-DA trade partner performance. Their appraisal? Overall, the DA partners knew the project better from the start, recognized schedule milestones, and understood the project’s non-negotiables. By comparison, non-DA trade partners struggled with complex details, schedule sequencing, and coordinating with other subcontractors.
Summation
Through the design assist project at Carnegie Mellon, our team found that the early involvement of contractors and fabricators in the design process enhanced communication, improved constructability, improved cost control, accelerated project delivery, and resulted in a more efficient allocation of resources. We are enthusiastic about the benefits our clients have seen from design assist, and excited about its potential to transform the construction industry.
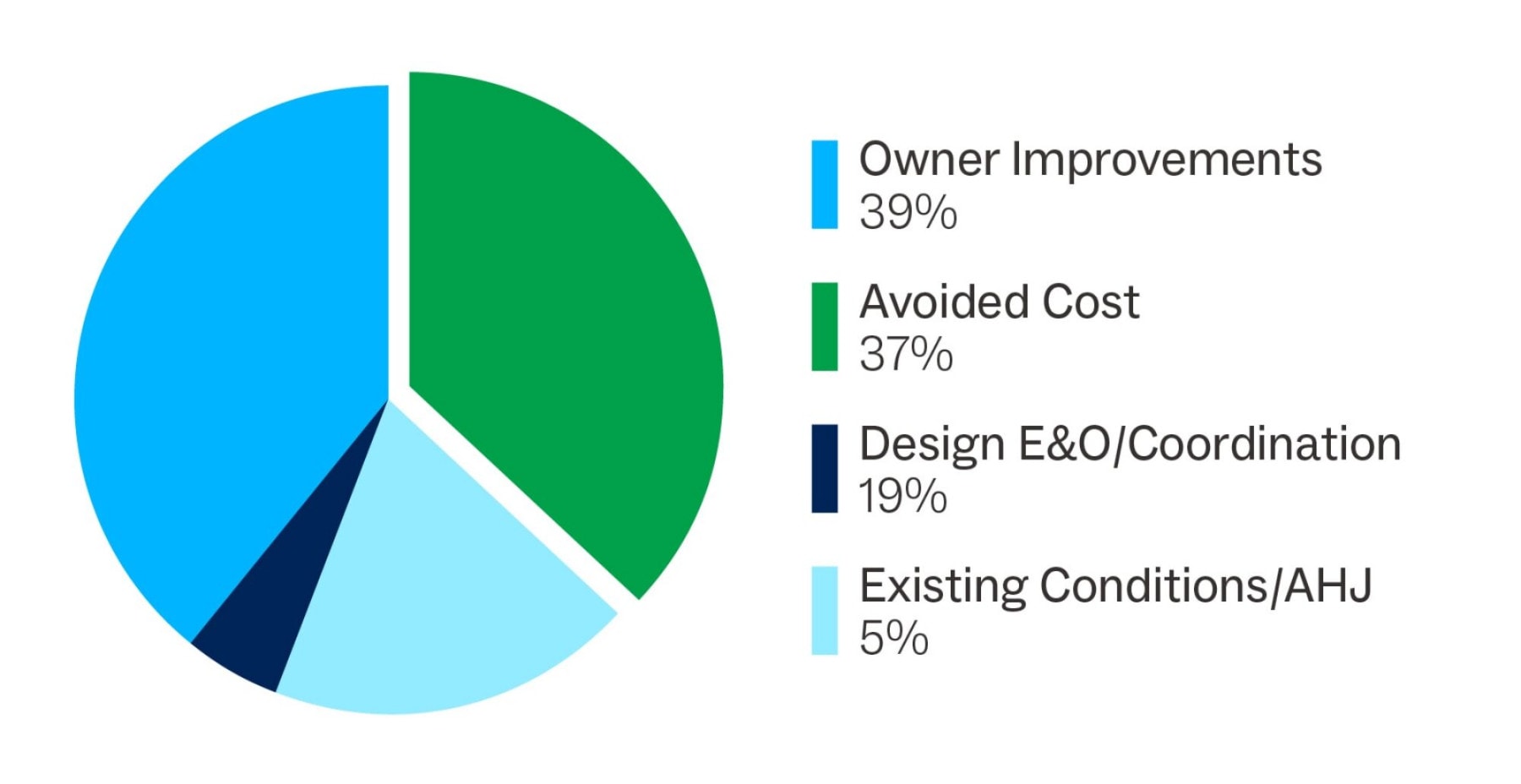